Costco's Cross-Docking Choreography
- The Costco Packaging Guys
- Mar 16, 2020
- 2 min read
Updated: Dec 1, 2020
You may have heard of cross-docking before but, what exactly is it? Why is it a significant competitive advantage to Costco and why is it essential that your packaging design flows seamlessly through this complex choreography?
Cross-docking involves unloading materials from an incoming truck at consolidation points and loading these materials directly into outbound trucks with little or no storage in between.
To clarify this process in the Costco world, when a 53' trailer with 60 pallets of your product arrives at a Costco depot (consolidation point), each of those 60 pallets are loaded onto up to 60 different trailers each destined to a Costco warehouse (destination point). This same process is simultaneously done with trailers from other product suppliers.

This process is amazing low touch, fast and ultra efficient. Although high value or large products may not flow through this same process, the majority of Costco products are cross-docked.
If this is such a great idea, why doesn't everyone switch to it? Certainly everyone in retail wants the efficiencies of cross-docking although Costco's business model, investments and processes have been built to optimize them. As an example:
Majority of products are merchandised on a full pallet level with standardized pallet sizes.
Costco warehouses are actual warehouses. This may seem obvious but, take a minute and look up next on your next warehouse visit. The pallet racks on the side aisles of every Costco location create a multi-level warehouse which allows significant storage.

While a Costco warehouse will have under 4,000 SKU, a typical Target location will have will have upwards of 80,000.
Costco has invested a significant amount of time to setup the cross-docking process and investment to keep it running. How we do ensure our packaging does not get in the way?
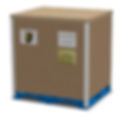
There are 3 ways main which packaging design and execution supports this process:
Structural integrity - Although the reduced touches of the cross-docking process does help reduce the possibility of damage, there is no time in this process for Costco to manage crushed trays or damaged pallets. During the structural design phase, the necessary pallet strength with proper safety factors based on the products must be considered. The structural design and/or materials will change based on the product size, weight and layout.
Outer pallet protection including corrugated shrouds, banding and stretch wrapping must ensure product doesn't lean or slide off the pallet. Outbound load are mixed with many different items. Don't assume what is placed on top of your pallet is going to be your load. Talk to an expert and get your pallet loads tested with all the ancillary packaging materials included.
Quantity of product - Designing your pallet to maximize the amount of product per pallet enables Costco to process a smaller quantity of pallets through the cross-dock process. Often, due to dollar value per pallet or sell-through concerns, you'll be asked to send in Feature Pallet displays full of fillers and void space. This is an entirely different challenge with structural design that needs careful consideration.
Finally, when delivering to a Costco depot, a dock appointment is needed through the Costco Portal. Delivering within this window ensures this ballet of pallet movement is possible.
Cheers,
TCPG